The Lusini Group is one of the leading hotel and catering suppliers in the non-food sector in Europe. Founded in 1987 as Hotelwäsche Erwin Müller, the group of companies headquartered in Wertingen, Bavaria, can look back on decades of history and now operates with around 650 employees at 14 international locations. Fast, smooth processes in the warehouse and for the warehouse management system are crucial for the omnichannel player.
Lusini uses the Erwin Müller warehouse management system, which was developed and implemented by TUP in 2009. This is a system that is individually tailored to the needs and requirements of the catering equipment supplier. Right from the start, mobile terminals (MDTs) were used in all functional areas of logistics, which are directly connected to the Erwin Müller warehouse management system to control the processes. Support for the previous MDTs with the Windows CE operating system has now been discontinued by the manufacturer and Lusini had to replace its end devices. For this reason, Lusini approached TUP to find a future-proof and economical solution for new terminals.
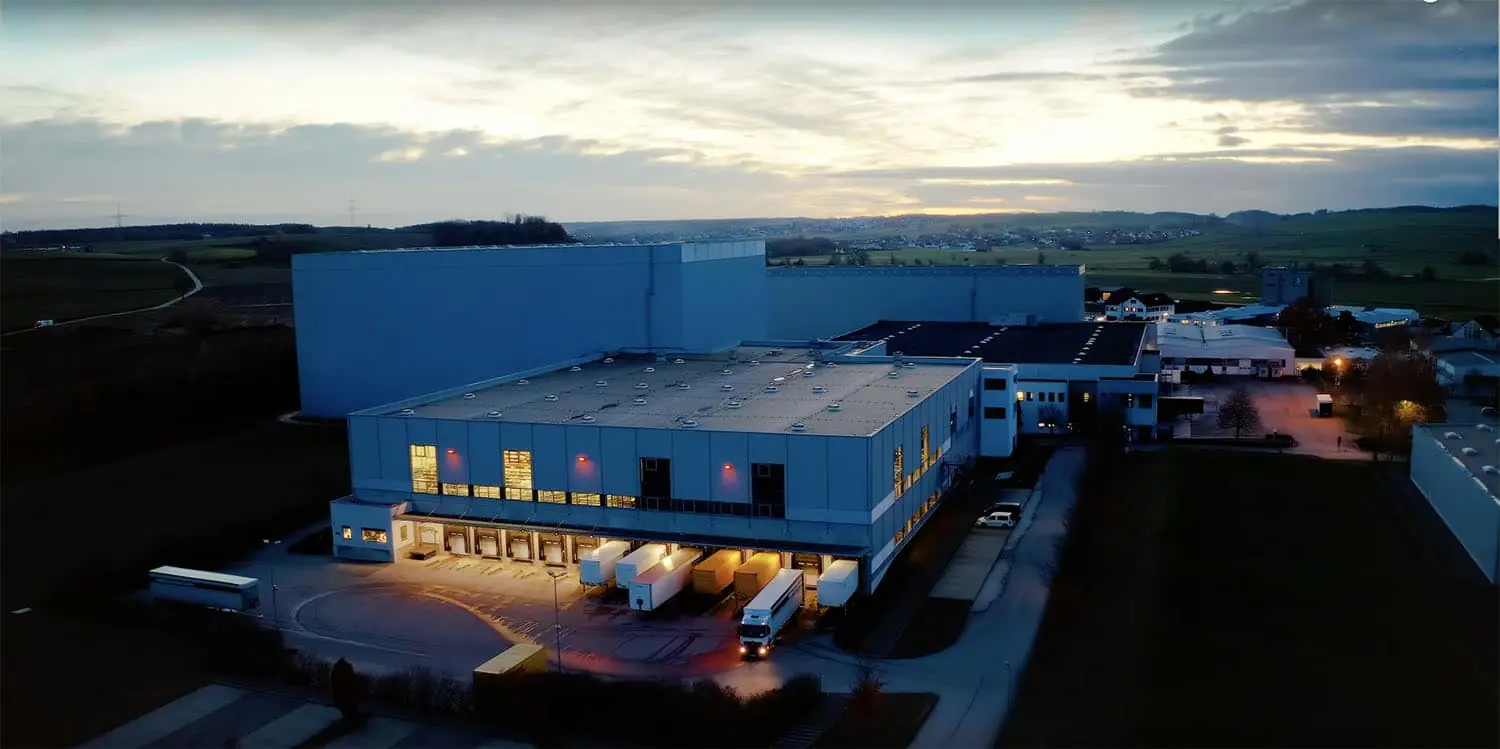
When selecting the devices, Lusini opted for Zebra devices, which were introduced in parallel to avoid a hard cut and ensure a smooth, low-risk transition. This meant that the previously used MDT devices continued to be used in parallel and were gradually replaced by new devices. Training bottlenecks and the corresponding need for additional training for employees were also to be avoided by transferring the dialog display in the respective process steps to the new device largely unchanged.
The solution - our modular approach with TUP.SML
With the modular software “TUP.SML” (Smart Mobile Logistics), android-based end devices for mobile data collection, including standard smartphones, can be used in the warehouse; headsets and ring scanners can also be connected using “TUP.SML”. This increases the number of supported mobile devices and the degree to which the respective processes are updated.
The application not only offers Lusini much greater freedom in the selection of suitable devices, but also further simplifications of a sustainable nature:
- Additional dialogs can be easily added.
- Graphic input and output elements can be displayed on the front end in a wide variety of constellations.
- Functional enhancements, such as taking photos and sending them directly to the warehouse management system as well as 3D representations of shelves with real-time occupancy, are also possible.
Integration during ongoing operation with an MDM system
TUP integrated the “TUP.SML” software package into the existing warehouse management system and ported the previous MDT application, including all existing MDT dialogs, to the Android system of the devices. The app was installed by the Lusini IT team, which relied on a so-called MDM (Mobile Device Management) system. This allows the app installation file to be distributed to all registered devices with a single click if desired. SML gives the customer a free choice and also offers a built-in update mechanism if the customer does not want to use MDM.
Minimal changeover for employees
The employees were effectively and safely introduced to the new device with the new software. For this purpose, “TUP.SML” was used to largely adopt the dialog display of the previous generation in the respective process step. During the development of the Android client for SML, great emphasis was placed on usability. User expectations were an important point that had to be met during implementation.
The daily use of a smartphone brings with it a certain amount of experience and therefore expectations as to how an app should be operated on a mobile device.
However, not all of these expectations could be met with the old dialogs. This resulted in the opportunity to translate old dialogs with the same or even more functionality into the new design and process language of the Android client. In some cases, this led to clearer, easier-to-learn processes. Existing features, such as acoustic signals for certain work steps, could be easily expanded. Parallel operation, which is possible at any time, was another challenge that was quickly solved thanks to the experience gained from numerous other projects.
Extensive functional and acceptance tests of the MDT processes in the test environment of the customer’s warehouse management system ensured that implementation could be carried out without impairing the availability of the logistics processes. The improved presentation of the dialog displays through text and coloring as well as acoustic signals for the respective employee during the execution of the work steps also ensured that the replacement of the MDTs ran smoothly and was a complete success.
To our references
Find out more about TUP.SML
Our latest blog posts
This article originally appeared in the special “Software and Automation 2023” of the specialist publication “Technical Logistics” and is available here as a PDF download in German.