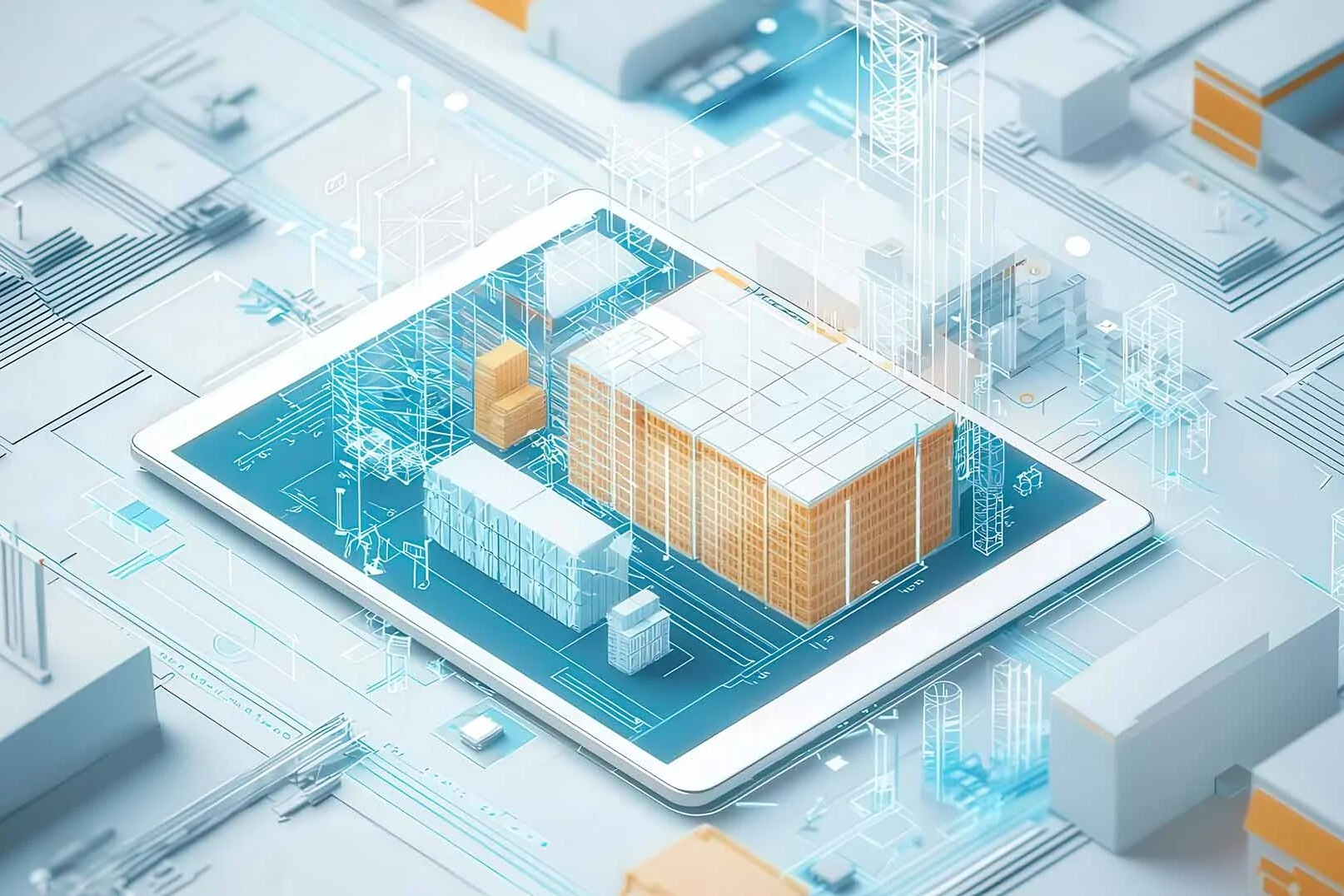
Project process
How we organize project phases
We go into depth and keep an eye on everything. Each stage results in a comprehensive deliverable that prepares the next phase in the best possible way. Be it specifications and requirement documents, test scenarios, sparring, planning or migration, we deliver performance, stability and long-term security.
Success Story
Breuninger combines three locations in a state-of-the-art multi-channel warehouse and opts for planning and software solutions by TUP
Previously, Breuninger handled store deliveries and direct customer deliveries via three logistics locations with a strict focus on either B2B or B2C. A new, large distribution center in Sachsenheim was to combine the previous locations. Both delivery variants were to be handled under the umbrella of a process-optimized multi-channel warehouse. Due to the demanding, individual processes, only modular, adaptive warehouse management software tailored to Breuninger was an option.
Success Story
TUP completed two large-scale projects for the bicycle manufacturer Canyon
A new production site with optimized intralogistics was created in a short space of time, enabling the switch from workstations to modern line production and the associated growth potential. As a follow-up project, a cross-location symbiosis of production and warehouse logistics was realized by TUP.
Over 40 years of experience in large-scale projects
An interdisciplinary team of logistics and software specialists
Our project managers have many years of cross-industry experience in the implementation of large-scale intralogistics projects – from goods receipt to goods issue. We attach particular importance to comprehensive testing and on-site user training for the system. Throughout, you will be supported by the very team that is developing your solution.
First Steps
During the planning phase, we work with you to develop the foundations for the successful implementation of your project. Our aim is to develop both a comprehensive specification sheet as well as one that is ready for implementation and approval.
Creating the specification sheet
The first crucial step towards the successful completion of the planning phase is the development of a market-ready specification sheet. We support you in defining your requirements so that they are formulated in a comprehensive, KPI-based and service provider-oriented manner.
Kick-Off Workshop
The aim of the kick-off workshop is to assess the existing situation and your requirements. On this basis, we can take all your needs into account for the next steps, answer open questions and get to know the status quo from your perspective and in your words.
Analysis and data collection
Data and its careful analysis form the basis for all subsequent phases. We use our project experience to go into depth where necessary. The data is then processed to be suitable for the project in question.
Evaluation of the target and current status
We compare the initial state with the target state in order to identify the most promising paths to your goal based on your specifications. Because individual requirements call for individual solutions.
Definition of KPIs per requirement
The success of a measure can only be reliably evaluated if all requirements are assigned a controlling KPI. We support you in identifying and defining project-relevant KPIs.
Identifying critical project variables
An overview of all project variables is the basis for success. Time and money are not the only parameters in intralogistics projects: we identify and prioritize all relevant values in order to optimally manage project developments.
Work breakdown structure
Complex projects require a clear, comprehensive work breakdown structure. Our experienced project managers will support you in creating it and ensure that all elements are defined and assigned.
Risk analysis
In addition to identifying and quantifying project risks, anticipating the future is particularly important for intralogistics projects. This is where you benefit from our proximity to research and our broad project experience.
Your project takes shape
During the implementation phase, we carry out extensive functional testing of software and hardware to ensure that end user feedback is integrated and support processes are in place effectively. We integrate our solutions tailored to your infrastructure.
Building the implementation architecture
To ensure the greatest possible security, our architecture consists of development, test, pilot and production systems.
Change Management
We support you and your teams during the introduction of the updated business processes during test and live operation. We use our expert knowledge to leverage the best possible optimization potential in these phases.
Definition of support workflows
Maintenance procedures and a rapid coordinated response in the event of a failure should not be first planned in the event of an emergency. We work with you to design and test standard and exceptional scenarios so that you can react quickly.
Functional testing of soft- and hardware
Our extensive test scenarios ensure that your intralogistics solution meets your KPIs at all levels and that your employees’ feedback is integrated.
Integration of user interfaces
Ultimately, it is up to the end users how well a system performs in practice. For this reason, we develop the user interfaces in close cooperation with your employees, from the shopfloor to the control center, on the basis of modular containers that are perfectly adapted to your processes.
Configuration and customization management
The coordinated interaction of individual technologies is the key to an efficient conveyor landscape. Thanks to our extensive system and market experience, we identify and tap into optimization potential as early as the implementation phase.
We go into detail
The test phase is the most important phase for us: here we create detailed test scenarios to minimize the risk exposure and incorporate the results of the integration tests directly into our adaptive software.
Training in the system
The team that developed your system will support you with training courses and workshops based on a train-the-trainer model. In this way, we ensure that your employees have the necessary system knowledge and that the interplay of processes is demonstrated transparently.
Individual training materials
To make your teams as efficient as possible during operation, we work with you to create detailed training documents to simplify onboarding and process optimization.
Process and user test
Together with your in-house logistics teams, we use various test scenarios to check whether the processes interact smoothly and whether your employees can run through the dialogs without any problems.
Laboratory and system tests, installation qualification
We accompany the installation of the system components and ensure that they are set up in accordance with the specifications and requirement documents.
Performance and load tests
After the accompanying quality assurance during the implementation phase, we test the system under load in collaboration with you and develop test scenarios that help us to identify and eliminate any problems before going live.
Migration testing
We are experts in migrations in green and brown field scenarios in a wide range of industries. We therefore carry out the necessary tests efficiently and in depth during this phase.
The system is online
We rely on continuous integration and testing to ensure that performance is not impaired during live operation.
Accompanying training by our project team
During live operations, we train your teams in the function of the system and the processes in the event of incidents. In this way, we ensure that the teams are fully familiar with the system in use and can react quickly to all relevant situations.
Operational Acceptance Tests
With our test scenarios, we go into depth here in order to carry out a detailed and documented operational acceptance test of the solutions used.
On-site support from our project team
Being on site guarantees the best response time. We are at the heart of the action during this critical phase so that we can make adjustments directly to the system and react quickly to unforeseen operating conditions.
We look towards the future
After implementation, we support you with quick adaptations to new business processes or market requirements.
Continuous support after implementation
Once the launch phase has been completed, we continue to support the project with our project team in the first few weeks in order to keep the reaction and customization speed high.
Sparring on an equal footing
The intralogistics market is constantly evolving. As experts with experience in this market since 1980, we provide you with an overview of new technologies and trends – always on a level playing field and individually adapted to your business processes.
24/7 support by the project team
We know that every minute in which your intralogistics is not fully operational costs a lot of money. That’s why we make sure that you get to the right contact person as quickly as possible and that the problem is well documented in the QA process.
Efficient adjustment and optimization cycles
The requirements for intralogistics are rarely static. Together with you, we review your solution with regard to optimization potential and IT security considerations.
Success Story
Planning of the central distribution center of Grass GmbH in Hohenems
TUP developed a customized Warehouse Management System (TUP.WMS) with an integrated Warehouse Control System (TUP.MFC) and new processes for the highly automated central distribution center in Hohenems.
Do you have any questions?